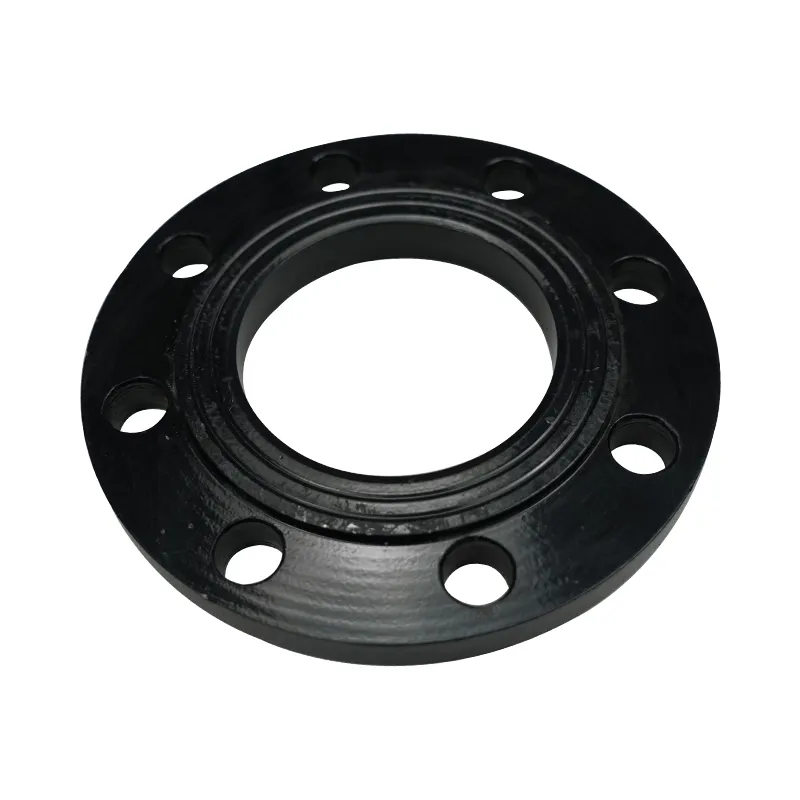
Introduction of Grooved flange pipe fittings
Grooved fittings include two broad categories:
①The pipe fittings that play the role of connection and sealing include rigid joints, flexible joints, mechanical tee, and groove flanges;
②The pipe fittings that play the role of connection and transition include elbows, tees, crosses, reducers, blind plates, etc.
The groove connection pipe fittings that play the role of connection and sealing are mainly composed of three parts: sealing rubber ring, clamp, and locking bolt. The rubber sealing ring located on the inner layer is placed on the outside of the connected pipe and is in line with the pre-rolled groove, and then a clamp is fastened on the outside of the rubber ring, and then fastened with two bolts. Due to the unique sealable structure design of the rubber sealing ring and the clamp, the groove connection has good sealing performance, and with the increase of the fluid pressure in the pipe, the sealing performance is correspondingly enhanced.
Features of Grooved flange pipe fittings
1. The installation speed is fast. The grooved pipe fittings only need to install the standard parts supplied and do not need subsequent work such as welding and galvanizing, so the installation speed is significantly faster than the threaded connection and flange connection, and the pipe can be automatically centered and aligned through the clamp. The construction efficiency can be greatly improved, and the pipeline installation period can be effectively shortened.
2. Safe and reliable. On the one hand, the grooving machine and hole opener used in the installation process are all special tools provided by the manufacturer, which can ensure the machining accuracy of the groove at the pipe end; Function, to achieve self-tightening sealing, the greater the internal pressure, the better the sealing. The nominal pressure of the fittings can be as high as 2.5MPa.
3. Easy to install. Grooved pipe fittings require a small number of bolts to be fastened and are easy to operate. Only a wrench is required for disassembly and assembly. Workers do not need special operating skills and can start work after training.
4. Economy. The grooved clamp connection will not damage the galvanized layer, and the pipeline does not need to be installed, galvanized, and transported again, so the installation cost is greatly reduced. Its installation speed is fast, which can shorten the construction period, make the project put into use in advance, and create economic benefits in advance.
5. Environmental protection. The piping and installation of grooved pipe fittings do not require welding or open flame operation, so there is no welding slag pollution, and no damage to the galvanized layer inside and outside the pipe, so it will not pollute the construction site and the surrounding environment and is conducive to fire prevention. Grooved connections reduce the transmission of noise and vibration due to the gap between the pipe ends.
6. It is not limited by the installation site and is easy to maintain. The grooved pipe fittings can be pre-assembled first and can be adjusted arbitrarily before the bolts are locked. The piping sequence has no direction. It can be operated in a relatively narrow working space and place. It can be cleaned and replaced only by removing 2 joints during maintenance.
Advantages of Grooved flange connecting
1. Simple operation
The connection operation of grooved pipe fittings is very simple, no special professional skills are required, and ordinary workers can operate it after simple training. This is because the product has incorporated a large number of fine technical parts into the finished product in a factory-like fashion. It only takes a few minutes to connect a pipe fitting, which greatly simplifies the technical difficulty of the on-site operation and saves man-hours, thereby stabilizing the project quality and improving work efficiency. This is also the general direction of the development of installation technology.
However, the traditional welding and flange connection pipeline connection method not only requires welding workers with corresponding skills, but also is time-consuming, and difficult for workers to operate, and there is pollution from welding fumes. Due to differences in operating space and welding skills, it is difficult to achieve satisfactory results in welding quality and appearance, thus affecting the overall quality of the project.
In addition, since the grooved pipe fittings are finished parts, the operation space required on site is small, and the installation can be realized against the wall and the corner, and the operation difficulty is greatly reduced, thereby saving the floor space and beautifying the effect of the pipe installation.
2. The original characteristics of the pipeline are not affected
For a grooved pipe connection, only a groove is extruded on the outer surface of the connected pipe with a rolling groove machine, without destroying the inner wall structure of the pipe, which is a unique technical advantage of a grooved pipe connection. Many pipes with anti-corrosion coatings on their inner walls would be damaged if conventional welding operations were used. Therefore, the specification stipulates that galvanized pipes, plastic-lined steel pipes, steel-plastic composite pipes, etc. shall not be welded and flanged, otherwise secondary treatment is required.
3. Conducive to construction safety
Using grooved pipe connection technology, only the cutting machine, rolling groove machine, and handle for tightening bolts are required on-site, and the construction organization is convenient. The use of welding and flange connection requires complex power cables, cutting machines, welding machines, oxygen, and acetylene gas cylinders, etc., which brings complexity to the construction organization, and there are hidden dangers of electric leakage and fire. . At the same time, the welding slag generated by welding and gas cutting will inevitably fall into the inside of the pipeline, and it is easy to cause pipeline valve parts and even equipment blockage during use, and also pollute the water quality in the pipeline.
In addition, welding and flange connection inevitably require long-term high-intensity aerial work, and production safety accidents are also prone to occur.
4. Good system stability and easy maintenance
The grooved pipe connection method has unique flexibility characteristics, making the pipeline anti-vibration, anti-shrinkage and expansion. Compared with welding and flange connection, the stability of the pipeline system is increased, and it is more suitable for temperature changes, thereby protecting The pipeline valve parts are reduced, and the damage to the structural parts caused by the pipeline stress is also reduced.
Due to the simple connection operation of grooved pipe fittings, the required operating space becomes smaller, which brings many convenient conditions for future maintenance. When the pipeline needs to be repaired and replaced, just loosen the two clamps to replace, rotate and modify a section of the pipeline at will. There is no need to damage the surrounding walls, reducing maintenance time and maintenance costs.
5. Economic Analysis
The connection operation of grooved pipe fittings is simple, labor-saving, and time-saving, so it has good economic benefits. Many articles have done economic analysis and believe that "with clamp connection, although the price of a single clamp is higher, the overall benefit of the entire pipe network installation is higher than that of flange connection". In the comparison of the article, the flange connection is treated by secondary galvanizing (this is also required according to the specification).